Understand the mystery of the transformer core and knowledge
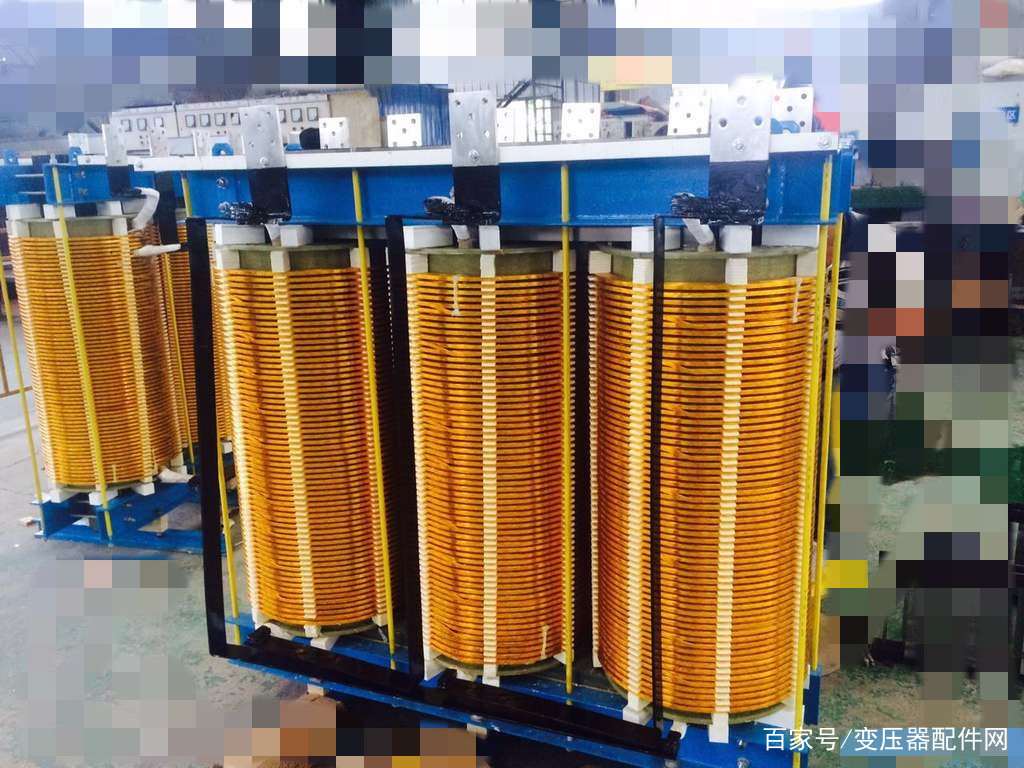
Power transformer is an indispensable part of the power system, it is responsible for the conversion of electric energy from one voltage level to another voltage level, in order to meet the needs of different power equipment. In the composition of the structure of the power transformer, the core is called the transformer “heart”, it is a key part of the magnetic circuit in the transformer, usually by the high content of silicon hot-rolled or cold-rolled silicon steel sheet stacked, coated with insulating varnish. The iron core and the coil wound on it form a complete electromagnetic induction system, which together realize the transmission and conversion of electric energy.
Working Principle and Function
01
Principle of operation
In the working principle, the magnetic conductor of the iron core is the magnetic circuit of the transformer, which is like a connecting bridge, turning the electric energy of the primary circuit into magnetic energy, and transforming the electric energy of the secondary circuit by its own magnetic energy, which is the medium of energy conversion.
02
Function
The main function is to fix and support the transformer windings and to provide a path that can transfer as much magnetic flux as possible. When alternating current passes through the transformer windings, an alternating electromagnetic field is generated, and the iron core conducts the magnetic field based on the principle of electromagnetic induction, thus increasing the ratio and efficiency of the transformer.
Composition and Classification
01
Composition
The core of a power transformer consists of three main parts: the core body, fasteners and insulation.
Iron core body is a magnetic conductor, usually by the high content of silicon hot-rolled or cold-rolled silicon steel sheet stacked together, these silicon steel sheet surface coated with insulating varnish, the formation of iron core stacked pieces. The core laminations are stacked or coiled in a specific way to form a closed path, which is not only the magnetic flux path for electromagnetic induction, but also the skeleton of the set coil.
Fasteners, on the other hand, include clamps, screws, glass ties, etc., which are used to hold the various parts of the core in place and ensure that it maintains a stable shape and structure during operation.
Insulation parts are mainly used to ensure the electrical insulation between the core and other parts to avoid dangerous situations such as electric shock or short circuit.
In addition, according to the different structure, the iron core can also be divided into two parts: iron core column and iron yoke. The core post is where the winding set is located, while the yoke connects the various parts of the core to form a closed magnetic circuit. This structure helps to increase the strength and stability of the magnetic field and improve the efficiency of the transformer.
02
Classification
The surface of the iron core is usually coated with a thin layer of oxide, which is used to prevent eddy current losses. Depending on the shape and structure, transformer cores can be categorized into different types such as E-type, I-type, C-type, etc. In addition, there are also triangular, pentagonal, toroidal and other shapes of iron cores.
The difference of the iron core is also a basis for the classification of transformers. According to the arrangement of the windings in the core, the transformer is divided into core transformer and shell transformer; according to the core of the number of phases and capacity, power transformers can be divided into single-phase transformers and three-phase transformers.
Frequently Asked Questions
01
Grounding problem
Due to uneven capacitance distribution, field strength varies, the core must be grounded, if not grounded, the core to ground suspended voltage will cause the core to ground intermittent breakdown discharge. Also note that only a point of grounding, if the core or its metal components have two or more points of grounding, will form a closed loop, resulting in local overheating, or even burn the core.
02
Material selection
In the transformer core material selection, generally use silicon steel sheet or nickel-iron alloy, the two application scenarios are different, everyday we are more familiar with the silicon steel sheet. Due to the high permeability of silicon steel sheet, it is commonly used in medium and low-voltage transformers, while nickel-iron alloy has a lower permeability, but high saturation magnetic induction strength, which is suitable for high-voltage transformers.
03
Common faults
Iron core multi-point grounding fault: one of the most common faults, multi-point grounding has many reasons, may be due to iron core burrs, metal foreign objects fall into, iron core and clamps or tank wall contact and so on.
Core short-circuit fault: Core short-circuit may be due to insulation damage between the silicon steel sheet, burr or metal foreign body caused by a short circuit. Short circuit will lead to local overheating, affecting the normal operation of the transformer, and may even cause fire and other safety accidents.
Iron core deformation failure: iron core deformation may be caused by the impact during transportation, improper installation or external forces. After the deformation of the iron core may make the winding and the core of the insulation distance between the short, or even lead to the winding and the core touch, triggering short circuit failure.
Loose iron core failure: loose iron core may be due to loose or fall off fasteners, core stacked pieces of insulation between the shim damage and other reasons. Loose iron core will lead to electromagnetic vibration and noise increase, affecting the stable operation of the transformer.
Iron core insulation damage failure: iron core insulation damage may be due to oil sludge, moisture and other impurities invade the inner core, resulting in insulation degradation. Insulation damage will make the electrical distance between the iron core and the winding or other metal parts become shorter, increasing the risk of short circuit.
For these common failures, the response to be done is to regularly inspect the transformer to prevent problems before they occur, such as the discovery of failures in a timely manner to repair.
04
Fields of application
In addition to power transformers, iron cores are widely used in inductors and magnetic materials. In inductors, iron cores can improve their inductance and quality factor, making inductors better able to store electrical energy. In magnetic materials, iron cores can enhance the strength and stability of the magnetic field by increasing the permeability of the magnetic circuit.